Today, most people will have a reference to the terms “Hybrid” and “Electric” from the car industry. The basic concept of one having an electric motor instead of combustion (Fully electric) and one being a combination of the two (hybrid) as main propulsion of the vehicle, has become common knowledge.
However, in practice the answer is a bit more faceted. Perhaps more so in the maritime industry, due to much higher power requirements, the unpredictability and demand of the environment of operation, and the subsequent safety considerations. Despite some challenges of technology limitations, electrification in the maritime industry is a pivotal step in the global efforts to reduce emissions while bringing operational cost down.
In this article we will take a high-level look at hybrid/electric technologies available today, elaborate on the challenges of transferring a market established by diesel engines to electric and hybrid solution, and the benefits that this brings to both the environment and your bottom line.
What is Hybrid and Electric?
As mentioned, due to the different power and safety requirements, you normally won’t find “fully electric” vessels performing the same range of tasks as a Diesel driven vessel. The main reason is the technology. Though advanced, it is still maturing, both in terms of capabilities and cost. Let’s start by going through the various configurations that comprises the two terms, Hybrid and Electric, in the maritime industry:
Hybrid:
- Diesel motor and an electric motor is connected to the same propeller shaft through a gear box, or to parallel drivelines. When to use one, the other or both is determined by the task, i.e., required load, duration, distance.
- Electric motor mechanically propels the vehicle, while a Diesel generator produces power that can either charge the batteries or supply additional power to the electric motor.
Electric:
- Electric motor is mechanically connected to the propeller, powered by batteries that are charged at quay.
- Electric motor is mechanically connected to the propeller, powered by batteries that are charged at quay. Additional power generator(s) can be present to provide power to ship systems to not affect range and capacity of the batteries.
The system as whole
Hybrid and fully electric solutions add some complexity to a system in a vessel. However, and even though it adds components and systems to a vessels already complex machinery, it is shown that both maintenance and running costs are lower for these state-of-the-art vessels.
Electrification involves integrating the following components/systems to your vessel:
- Battery
- Battery Management System (BMS)
- Electric motors
- Power Management System (PMS)
- Energy Management System (EMS)
- Propulsion control system (PCS)
- Human Machine Interface (HMI)
- Industrial Automated Systems (IAS) - Alarms and automation
- Gear box designed for either Hybrid or fully electric applications.
- Propellers (Fixed or Controllable pitch) for optimizing efficiency across speeds and loads.
- Digital solutions for remote assistance
All these components often have different manufacturers and abilities, depending on the intended use (the operational profile) of the vessel. System integrators specialise in optimising the configuration of these systems. The integration with the mechanical elements of the ship must be efficient and seamless. It is a balancing game that requires deep knowledge of a vessels physical properties, the individual systems and how it all communicates with each other and externally.
Available technology
One of most important components, and perhaps the biggest challenge when it comes to marine electrification is the battery technology. Batteries are commonly defined as two types, ‘Power’ or ‘Energy’. This means that, per kilo of battery you will either have properties that allow it to deliver a lot of power for a short time, or smaller amount of power for a long time. Different battery-technologies varies in how fast they can be charged and how much power it requires to charge it. Furthermore, this is proportional to how much power it can/must be able to deliver and for how long. Only to a limited degree can you get the best of both worlds.
New technology, new considerations
These battery properties adds a new consideration for operators of marine vessels: charging infrastructure. Hydrocarbon fuel has an established infrastructure and a higher energy density. This has made fuelling relatively easy for diesel vessels. For fully electric vessels, the frequency of charging your battery is higher than fuelling diesel. You can also always drive a tanker truck down to the piers, but High Voltage charging stations are still not common. These also rely on the local grid capacity, introducing a new consideration to the industry. There are exciting new battery chemistries and designs being developed, but these are still experimental and not yet available on an industrial scale.
This is a great simplification of the challenges of electric solutions at sea, but illustrates how your operation, the vessel’s intended use and the region it operates, define the optimal solution.
Your operational profile decides
A fully electric, zero emission, solution can be challenging. If the intended operation is many short trips, you will need different technology and components than if the ship needs to go larger distances, operate in open waters, or haul heavy cargo. The power/propulsion requirements of a specific operation define, down to the component level, what you will need. A major change of the operational profile will require a retrofit of components and their configuration.
There are no clear rules, but the main indicator of whether your vessel can go fully electric or need a hybrid solution is predictability:
- If the vessel’s intended operation is a very predictable route, in generally calm/stable waters, a fully electric is fairly straight forward. This is why you often will see fully electric passenger ferries or sightseeing cruises.
- If the ship must be able to provide a wide range of tasks, at unpredictable destinations, stops and prediction, then Hybrid is the optimal choice to reduce emissions. Examples: CTVs and search and rescue vehicles.
It is important to emphasize that the scope of electrification should be based on your needs. System integrators and yards with in-depth knowledge of your industry and operation should be able to set limits and provide you only what is needed.
Emerging capabilities and benefits
There are as you can see considerations and challenges that are new to the marine industry, but the benefits of partial or full electrification are substantial. Efficiency and lowered emissions are only the tip of the iceberg:
- Components are easier to maintain.
- Digital systems provide a level of data on your operation not before possible, providing the foundation of optimising your whole enterprise, not only the operation of the electrified vessel.
- Reduced market uncertainty and risk by being a more attractive choice/prospect for both customers and investors.
- Lower fuel consumption and operational cost.
- Tax benefits and incentives for operating a low/zero-emission vessel.
- Safety and operational stability.
- More EHS friendly atmosphere with less noise.
- Future Resell value of the vessel.
- compliance with emerging emission regulations locally.
With wider adoption of hybrid / electric solutions at sea and its further development, the impact of these attributes will only increase, while both cost and flexibility of the technology will improve.
Conclusion
The choice of solution for electrification, be it hybrid of fully electric, is determined by the intended operation of the vehicle. Low/zero-emission vessels are not capable of every task at sea. This is due to the limitations of battery technology and the high safety requirements in this sector. Furthermore, the much higher power requirements, the unpredictable operational environment at sea and the subsequent safety considerations all present challenges.
The optimal choice of solution, i.e., Hybrid or fully electric, and in what configuration, is determined by the intended operation profile of the vessel. These are tailored systems, which require a system integrators in-depth knowledge of all components and their interfaces. However, a gradual upgrade path or electrification at a limited scope, is possible.
Despite the challenges and new considerations for the industry, the benefits of electrification are immense. In the short-term you find a higher level of safety and the reduced OPEX of having an efficient vehicle. In the long term you can gain both knowledge and capital from the data ships system can provide, the lowered maintenance cost. Most of all, you are making a difference for the environment and have a future-proofed vessel for any regulatory measures.
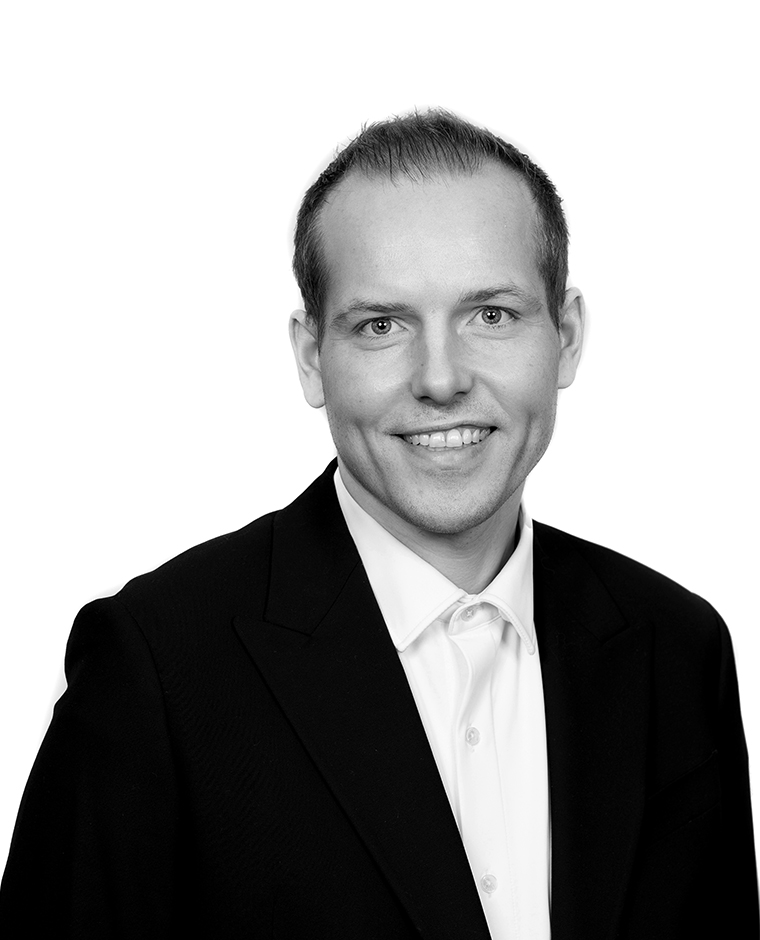